GREEN CASTING SERVICES
The Super Vac Foundry offers green sand casting services, a process that uses green sand — a combination of olivine sand and bentonite clay — to create molds for metal castings. Green sand casting is ideal for both low- and high-volume specialty parts, and while extremely custom, more than 80% of all metal castings are produced using this process.

• 319 Aluminum (319SR)
• 356 Aluminum (356.2)
• 535 Aluminum (535.2)
• 713 Aluminum (713.1)
• 771 Aluminum (771.2)
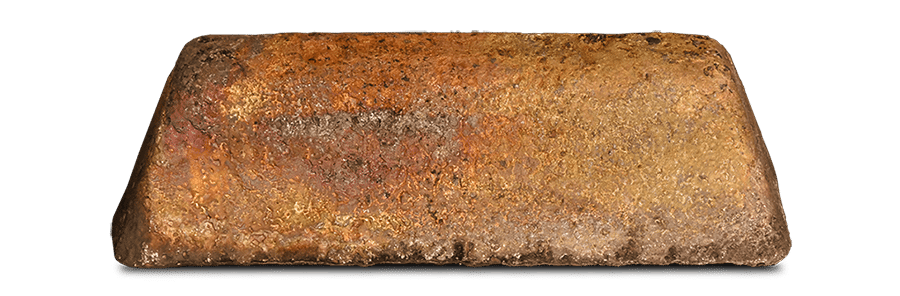
Offering brass alloy components:
• Red Brass Alloy (115)
• Manganese Bronze (421)
• Silicon Bronze (500)
STEP 1A THE SAND MOLD IS CREATED
First we source a 3D printed pattern, a replica of the part that will be cast. This pattern is placed into the molding box, also known as a casting flask. Sand is then packed around the pattern through a vibratory process, called ramming. Eventually, the pattern is removed, leaving behind the sand mold.
STEP 1B OPTIONAL “CORES” ARE CREATED
Once the sand mold has been made, aluminum or brass is melted in the furnace. Super Vac'S largest furnace can hold up to 600 lbs. of metal while reaching 1,200-2,200° F. The molten metal is then poured into the mold using a ladle and left to cool for 10 minutes. After cooling, the mold is broken to reveal the casting, and the sand is recycled through the process again.
The final step in the sand casting process often involves grinding, sanding, polishing or machining the component to achieve the desired dimensional accuracies, physical shape and surface finish. The Super Vac Foundry has a dedicated finishing mill to create polished parts, as well as five CNC machining centers to deliver turn-key products. Click here to learn about our machining services.
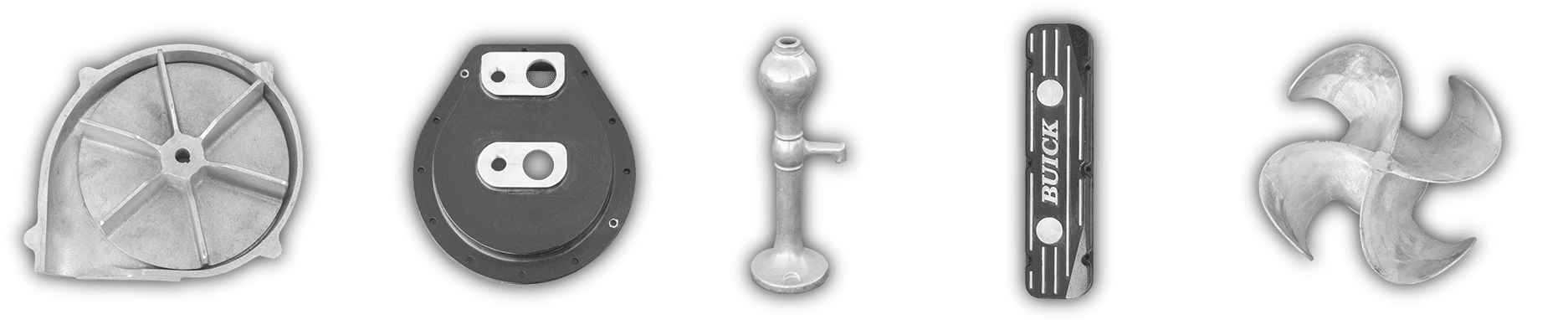
LOOKING FOR METAL CASTING SERVICES?