SHELL MOLDING SERVICES
For high production rates and superior dimensional accuracy, customers look to Super Vac’s shell molding services. This process delivers an expendable mold used to cast aluminum parts. The mold is made from a thin “shell” of resin sand that is broken apart to reveal the cast part. Super Vac offers the largest shell core machine in Colorado, which can accommodate core boxes that weigh up to 2,500 lbs.

• 319 Aluminum (319SR)
• 356 Aluminum (356.2)
• 535 Aluminum (535.2)
• 713 Aluminum (713.1)
STEP 1 THE SHELL MOLDING PROCESS
STEP 2 THE SHELL CASTING PROCESS
Once the two shell halves have been created, they are clamped together and placed into a pouring flask to form the complete shell mold. (During this step, shell or CO2 cores can be inserted to create hollow parts.) Molten metal is then poured into the shell mold cavity and left to cool, solidifying into the final casting. After the metal has cooled, the casting is removed by breaking the shell mold.
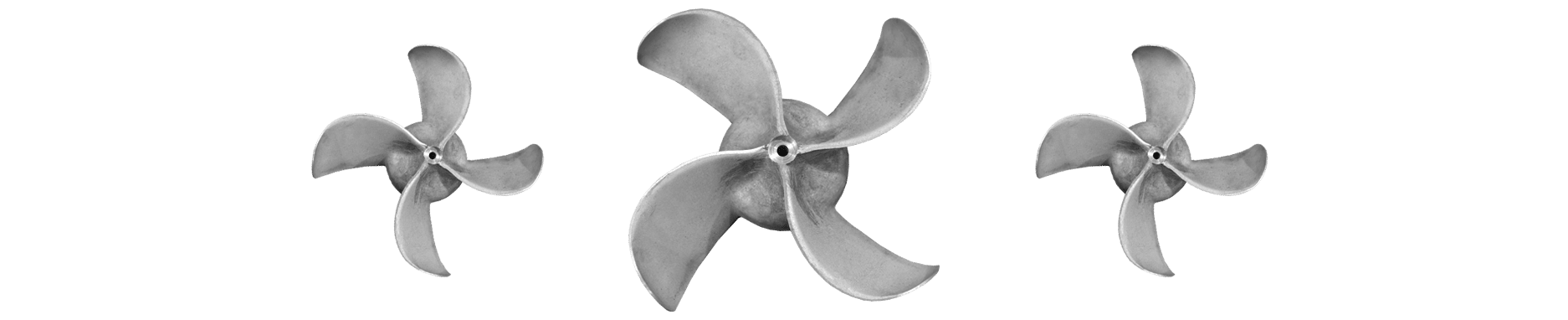